High Precision Metal Stamping in New Energy Vehicle Battery Manufacturing
Precision metal stamping plays a crucial role in the mass production of safe, efficient, and high-performance batteries for electric vehicles (EVs). As global demand for EVs continues to rise, the technology’s ability to create complex, compact components with micron-level accuracy has become essential.
Key Applications of Precision Metal Stampings in NEV Batteries
Cell Housings & Caps
- Function: Seal lithium-ion cells; manage thermal/electrical conductivity.
- Stamping Requirements:
- Ultra-precise deep drawing (±0.05mm tolerance) of aluminum/stainless steel.
- Burr-free edges to prevent internal short circuits.
- Surface treatments (e.g., laser cleaning) for weld compatibility.
Busbars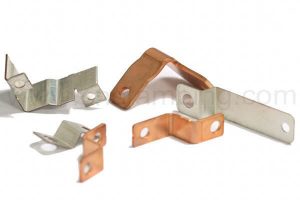
- Function: Transmit high currents between cells/modules.
- Stamping Innovations:
- Micro-stamping of ultra-thin copper/copper-clad aluminum (0.1–0.3mm).
- Coining for low-resistance contact surfaces.
- Progressive dies for integrated features (e.g., fusing points, sensor mounts).
Thermal Management Plates
- Function: Regulate battery temperature via liquid cooling.
- Stamping Solutions:
- Complex channel geometries stamped into aluminum sheets.
- Vacuum brazing-ready dimensional stability.
- Corrosion-resistant coatings (e.g., anodization).
Battery Enclosures & Structural Parts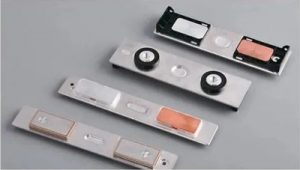
- Function:Protect cells; integrate with vehicle chassis.
- Stamping Advances:
- High-strength steel (HSS) and aluminum alloys for lightweight crash protection.
- Multi-stage stamping-bending-welding hybrid processes.
- EMI-shielding features for electronics safety.
Technical Challenges & Innovations of Precision Metal Stamping
- Material Science
- Stamping high-conductivity alloys (e.g., C11000 copper) without cracking.
- Adopting clad materials (e.g., Al-Cu) to balance conductivity/weight.
- Precision Demands
- Vision-guided progressive dies for ±5μm positional accuracy.
- In-line laser measurement for real-time thickness/geometry validation.
- Sustainability
- Scrap reduction via AI-optimized nesting (e.g., achieving >85% material yield).
- Closed-loop recycling of metal offcuts.
Industry Trends Shaping Development of High Precision Metal Stamping Service
- Solid-State Battery Integration
- Stamped bipolar plates for solid-state cell stacking.
- Hermetic sealing solutions for sulfide-based electrolytes.
- Cell-to-Pack (CTP) & Cell-to-Chassis (CTC) Designs
- Larger, functionally integrated stamped components.
- Stamped cooling/structural composite parts.
- Automation & Industry 4.0
- Servo-press synchronization with robotic pick-and-place.
- Digital twins for predictive die maintenance.
Market Impact
Cost Reduction: Stamping cuts cell manufacturing costs by ~15% vs. machining.
Scalability: Enables production of 10,000+ parts/hour for gigafactories.
Supply Chain: Localized stamping hubs emerging near EV plants (e.g., Tesla’s Texas Gigafactory).
Conclusion
Precision metal stamping plays a key role in advancing electric vehicle (EV) batteries, optimizing performance, safety, and manufacturability. As we embrace new battery chemistries like sodium-ion and silicon anode, stamping technologies will evolve to meet demands for thinner materials and tighter tolerances while promoting sustainable mass production. Collaboration among leading companies—press OEMs such as Schuler and Komatsu, material suppliers like Novelis and Aurubis, and battery manufacturers including CATL and LG Energy Solution—is crucial to foster innovation and propel the industry toward a brighter, more eco-friendly future. Let’s drive this exciting journey together!