How to Choose a Suitable Automotive Terminal Pins Manufacturer
Terminal type and terminal plating play a vital role in the design of automotive wiring harnesses. Reasonable selection of terminal type and plating material can improve the reliability and stability of the wiring harness and ensure the normal operation of the automotive electronic system. In the process of wiring harness manufacturing, when selecting a manufacturer, more attention should be paid to the control of material selection, processing and connection quality. Only reasonable and appropriate processing methods and connection methods can improve the reliability of terminal connections. At the same time, attention should also be paid to front-end and back-end services, strengthen the quality inspection and verification of terminal connections, and promptly discover and deal with problems to ensure the reliability and stability of the wiring harness.
Choosing Automotive Terminal Pins suppliers: Insight into the Differentiated Value of Manufacturers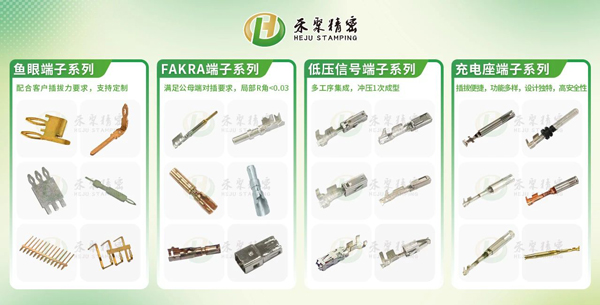
In the highly specialized and demanding field of automotive wiring harness terminals, the choice of suppliers is directly related to the performance, reliability and stability of the product supply chain. Many suppliers can provide products that meet the “standard”, but the reason why Heju Precision can stand out and become the core automotive terminal pins partner of the top configuration of popular models such as BMW, Wenjie, Xiaopeng, and Geely is that the core lies in a series of internalized unique capabilities and commitments. These qualities permeate every link of its service, production and quality system, forming a competitive advantage that is difficult to replicate.
Service: Deep Collaboration of “Engineering Partners” Beyond Order Delivery
Heju Precision’s service concept does not stop at “supply on demand”. Its uniqueness lies in the establishment of a collaborative mechanism that is deeply embedded in the customer’s R&D and production processes:
- Front-end intervention and joint development
Heju’s team of senior application engineers is accustomed to actively intervening in the early stages of customer product design. Not only receiving specification requirements but also providing manufacturability design optimization suggestions based on a deep understanding of material properties, stamping process limits, and connector matching trends. This avoids frequent mold repairs, delays, and cost increases caused by design defects in the later stage and significantly improves the overall efficiency and success rate of customer projects. This “preventive service” thinking is difficult for suppliers who simply follow the map to provide.
- Transparent communication and active warning
Heju advocates information transparency. Instead of passively waiting for customer inquiries, it actively establishes a supply chain health monitoring and potential risk warning mechanism (such as fluctuations in key raw materials and prediction of production capacity bottlenecks) and communicates plans with customers in a timely manner. This proactive management attitude of “treating customer problems as one’s own problems” provides additional guarantees for the stability of customer supply chains.
Production: Meticulously Crafted “Micron-Level Control” and Vertical Integration Advantages
Heju Precision’s core competitiveness is rooted in its ultimate pursuit of ultra-high precision stamping technology and vertical integration of key links:
In the field of automotive wiring harness terminals, micron-level precision differences directly affect conductivity, plug-in force and long-term reliability. Heju’s core advantage lies in its mastery of continuous die-stamping technology through self-developed high-precision molds and real-time precision monitoring of equipment status. This control of the “micron world” is the physical basis for its product consistency and reliability, which is far from being achieved by imported equipment alone.
- The deep control brought by vertical integration
Heju is not a simple processing plant. Its design and manufacturing capabilities for core molds are the core of its uniqueness. Having a self-made mold team means faster response and iteration: mold modification and optimization do not need to rely on external suppliers, and the cycle is greatly shortened.
- Deeper process understanding and optimization
The accumulation of the entire process of designing, manufacturing, and repairing molds is transformed into deep insights into core process parameters such as product form, material flow, and life prediction, which can continuously optimize production efficiency and product performance.
- Deep integration of material science and technology
Heju not only focuses on stamping but also has a deeper understanding of the decisive influence of material properties (such as elastic modulus, yield strength, and conductivity of copper alloys) and surface treatment processes (such as coating thickness, uniformity, and adhesion) on the final performance of terminals. The internal process continues to cross-validate materials-process performance to ensure that the material selection and process parameters can accurately match customers’ stringent requirements for electrical performance, mechanical strength, corrosion resistance, and weldability.
Quality: “Zero Defect” Culture Internalized in Genes and Customer-Driven Continuous Improvement
For Heju, quality is not an isolated set of inspection standards but a culture and operating method that is integrated into the blood of the enterprise. The high customer satisfaction it brings comes from:
- Preventive quality system of “getting it right the first time
Heju’s quality management focuses on the front. The powerful APQP (Advanced Product Quality Planning) process ensures that risks are systematically identified and control plans are formulated from the start of the project. Statistical process control is deeply applied to the entire production process rather than relying solely on final inspection. This means that quality is “manufactured” rather than “inspected”, which fundamentally reduces the defect rate.
- “Zero Defect” pursuit beyond AQL
Although the industry generally accepts the AQL level based on sampling inspection, Hoju has set process control targets (such as Cpk values) that are far higher than customer contract requirements. Its online full inspection or high-frequency sampling of key dimensions, as well as its strict monitoring of process stability, reflect its actual pursuit of “zero defects” rather than just slogans. This self-pressure directly translates into lower PPM values and higher production line pass rates for the client.
Conclusion
Choosing Heju Precision means not only choosing a automotive terminal pins supplier but also a long-term strategic partner with a profound engineering background, meticulous manufacturing capabilities, and a core belief of “zero defects”!