7 Kinds of Stainless Steel Deep Drawing Problem Solutions
Stainless steel has a low elongation rate, a large elastic modulus E, and a high hardening index. The cracking of stainless steel drawing parts sometimes occurs after the drawing deformation, sometimes when the deep drawing part is withdrawn from the die matrix; sometimes it occurs when it is impacted or vibrated after drawing deformation; sometimes it occurs after a period of storage or during use after drawing deformation.
What are the Common Problems in the Stainless Steel Deep Drawing Process?
1. Surface Crack
Austenitic stainless steel has a high cold work hardening index (stainless steel is 0.34). Austenitic stainless steel is meta-stable and undergoes phase transformation during deformation, which induces martensite phase. Martensite phase is brittle, so it is prone to cracking. During plastic deformation, as the amount of deformation increases, the content of induced martensite will also increase with the increase of the amount of deformation, and the greater the residual stress. The relationship between residual stress and martensite content:The higher the martensite phase content induced, the greater the residual stress caused, and the easier to be crack during deep drawing processing.
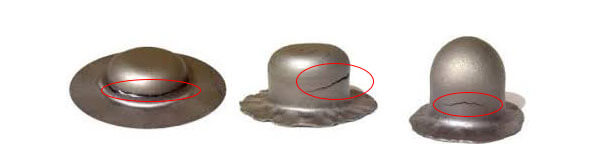
2. Surface Scratches
The scratches on the surface of stainless steel deep drawing parts are mainly due to the relative movement between workpiece and the tool surface. Under a certain pressure, the blank strip and the local surface of the mold are directly friction, and the deformation heat of the material strip causes the metal strip and metal chips to be deposited on the tool surface, and result in the scratches on product surface.
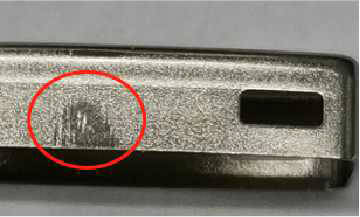
7 Kinds of Stainless Steel Common Forming Defects Prevention Measures:
1. Choose the right stainless steel material: the commonly used materials in austenitic stainless steel are 1Cr18Ni9Ti and 0Cr18Ni9Ti. In the deep drawing process, 1Cr18Ni9Ti is more stable than 0Cr18Ni9Ti and has better crack resistance. Therefore, it’s better to choose 1Cr18Ni9Ti material while make deep drawing parts.
2. Choose correct tool material: Stainless steel hardens significantly during deep drawing process, it producing many hard metal points which adhesive on part surface, making the workpiece and mold surface easy to be scratched and wear. Therefore, there advise use the copper-based alloy tool, which can eliminate scratches and dents on deep drawing part surface and reduce the damage rate. Another qualified material is high-aluminum copper-based alloy tool material (containing aluminum 13Wt%~16Wt%), which has low mutual solubility with SUS304 stainless steel, no adhesive between deep drawing parts and tool surface, which reduce the product surface scratch risk and product polishing cost, it’s already been successfully applied in the field of stainless steel deep drawing. However, due to the low hardness of this kind of mold (40HRC~45HRC), it is often used to produce relatively small thickness t/D products. Generally, after 1500 to 2000 pieces are deep drawn, it is easy to produce radially drawn edges starting from the round corner R on the surface of the die. Now Silicon nitride ceramics (Si3N4) have become important engineering materials, especially reaction sintered silicon nitride ceramics, which have good high&low temperature mechanical properties, thermal shock resistance and chemical stability,and can be easily made into complex components. Then there can use the high hardness, high wear resistance and high chemical stability of ceramic material and Reaction sintering silicon nitride die to instead of common SUS304 deep drawing die.
3. Choose reasonable punch and die inserts fillets: The die inserts fillet has a great relationship with the stress size and stress distribution. The fillet radius is large, and the blanking holder pressing material area is insufficient, which easy be instability and wrinkles. If the fillet is too small, the resistance of the material into the die inserts during the deformation process will increase, and the material will not easily flow and transfer inward, then increase the maximum tensile stress in the force transmission area, which may cause tensile cracks. Therefore, it is very important to choose a reasonable radius of punch and die inserts radius fillets. When the rp/t value approximately 4, it can help prevent cracking. The punch and die inserts fillets increase, and the extreme deformation will increase. When the die inserts fillet is 5mm to 8mm, it is helpful to prevent cracking.
4. Use thinning deep drawing method: Previous researchers have also proved through experiments that using thinning deep drawing method can greatly reduce the maximum value of the tangential residual stress of the deep drawn parts and effectively prevent longitudinal cracks from occurring. According to the different degree of deformation and the thickness of the original sheet material, should choose the appropriate thinning factor Ψn (generally 0.9t~0.95t). If the value of Ψn is too small, the deformation stress will increase sharply, which will cause the bottom of the deep drawing part to crack.
5. Adding an intermediate annealing process to the deep drawing process: It can completely eliminate residual stress and restore the structure of austenitic stainless steel. For high hardness stainless steel, intermediate annealing is required. Such as 1Crl8Ni9Ti, usually the heating temperature is 1150℃~1170℃, the heating time is 30min, and it is cooled in airflow or water. In addition, the heat treatment is better to make after deep drawing, which can avoid deformation or cracking which caused by internal stress action during long time storage
6. Use appropriate lubricants: use appropriate lubricant have good performance during make stainless steel deep drawing parts. The lubricant can form a film with a certain degree of toughness and elongation between the punch and die inserts, which can help to deep drawing of stainless steel parts. For difficult forming deep drawing parts, polyvinyl fluoride film can be used as a lubricant in actual production. Polyvinyl fluoride film has excellent tear strength, certain toughness and elongation, and is easy to clean after stamping. After the dry film is coated, the dry film can deform together with the product during the deep drawing process, and the product can always be separated from the mold. In addition, the film itself has a certain porosity and a large number of fiber cracks, so a certain amount of lubricant can be stored, so the film Equivalent to a layer of dry film lubricant. This lubrication method can effectively isolate the deformed stainless steel plate from the tool surface, and has a good lubrication effect, which is help to improve the tool life time and product pass rate.
7. Other preventive measures
The following preventive measures can also be taken in stainless steel deep drawing processing:
(1) The white cast iron has good oil storage performance, it is easy to form a lubricating oil film during processing, then the blank holder could use white cast iron material;
(2) use tapered blank holder Circle;
(3) Tool inserts edge smooth machining, have no micro cracks.
In case you have any question about deep drawn stamping, feel free to contact Heju.